高效能全方位优化:PDPS仿真软件智造工业革新新境界
19429202025-03-21驱动程序13 浏览
一、传统制造业转型,为何总被“试错成本”拖垮?
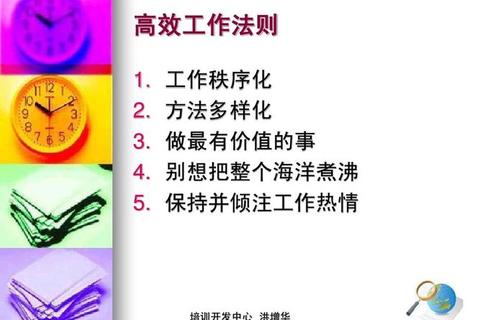
在长三角某汽车工厂里,工程师们正在为新的焊接产线投产焦头烂额——机器人轨迹干涉导致设备损坏,节拍计算偏差引发产线堵塞,这些问题让项目延期三个月,直接损失超2000万元。这个场景折射出中国制造业的集体困境:实体设备调试如同“开盲盒”,试错成本吞噬着企业利润。
当全球工业4.0浪潮席卷而来,“高效能全方位优化:PDPS仿真软件智造工业革新新境界”正在改写游戏规则。西门子旗下这款数字化工艺平台,用虚拟世界预演现实生产,让机器人在比特空间里完成百万次碰撞实验,将传统需要3个月的调试周期压缩至72小时。
二、产线设计能否告别“纸上谈兵”?
东莞某家电企业引入PDPS后,工程师在虚拟环境中搭建出完整的空调装配线。通过Process Designer模块,他们将CAD数据与工艺逻辑深度融合,自动生成包含132个工位的三维动态流程图。系统智能识别出7处潜在干涉点,并给出3种优化方案,使产线空间利用率提升23%。
这种“数字孪生”技术突破传统二维图纸局限,支持CATIA、UG等主流三维格式直接导入。更令人惊叹的是,软件内置的节拍计算器能精确到0.1秒,某新能源汽车企业借此将焊装车间节拍从52JPH提升至68JPH,年产能增加12万辆。
三、机器人调试真需要真人“刀尖起舞”?
长安汽车某焊接车间曾发生惊险一幕:调试中的机械臂突然失控,距工程师仅20厘米急停。而使用PDPS的虚拟调试功能后,技术人员通过PLCSIM Advanced模块,在电脑上完成全部128台设备的信号联调。系统自动生成的碰撞热力图,精准定位出传送带与AGV小车的5处轨迹冲突。
Process Simulate模块更支持KUKA、ABB等9大品牌机器人离线编程。某电子代工厂为苹果生产线调试时,直接导出机器人控制代码,现场调试时间从28天缩短至3天,良品率反而提升0.15%。这种“高效能全方位优化:PDPS仿真软件智造工业革新新境界”,正在重构人机协作的安全边界。
四、人机工程优化只能靠老师傅经验?
在吉利某总装车间,PDPS的人因工程模块揭开惊人真相:原设计工位使工人每天需完成132次蹲起动作,腰椎负荷超标3.7倍。软件通过生物力学分析,重新规划工具架高度与工件流转路径,使人体姿态优化度提升61%,年减少职业损伤赔偿金380万元。
这种量化分析能力延伸至全价值链。某飞机制造商运用该软件的工时分析系统,将舱门装配动作分解为58个标准单元,通过动作经济性原则重构工序,使单件工时从43分钟降至29分钟,年节约人工成本2700万元。
破局之道:三步构建数字智造护城河
对于渴望突围的制造企业,建议分阶段实施:首先建立跨部门的数字化小组,选择总装或焊装等关键工序试点;其次配置CATIA+PDPS+Teamcenter数据链,确保三维模型到工艺数据的无缝流转;最后培养既懂工业工程又精数字工具的复合人才。
“高效能全方位优化:PDPS仿真软件智造工业革新新境界”不是未来科技,而是当下必须抓住的生产力革命。当虚拟调试使设备利用率突破85%,当数字孪生让新品导入周期缩短60%,那些率先拥抱这场变革的企业,正在智能制造的新赛道上建立起难以逾越的竞争优势。